The Propeller Saga
Last year, we bought a new Flexofold, two blade, folding propeller to replace the old feathering propeller which was a bit weak and did not always turn to the correct position when reversing. In the past folding propellers were known to produce almost no thrust in reverse with massive amounts of prop walk. According to a test carried out by Yachting Monthly that issue has been improved significantly. They found the forward power of a two blade Flexofold to be equivalent to a fixed prop and it still had 80% of the thrust in reverse as compared to a fixed one.
Unfortunately, we did not have the time to put the propeller on to the boat before it was put back in to the water, so we had to make do with the old one for one more season.
With the boat on the hard, we assumed it would be a simple job of placing the new propeller on the end of the shaft and tightening the bolts.
Of course, that would be way to easy!
On the first attempt to put the hub on the shaft, I quickly realised there is no chance it will fit. The bore is way to small and will never fit. It turns out I mistakenly ordered a propeller for a 22 mm shaft when we have a 30 mm shaft. Since I had hardly taken the hub out of its packaging, I sent it back to Flexofold in Denmark, and they sent the correct size back.
Now it should fit right?
Well, the hub fits onto the shaft now, so now it just needs to be fixed on with the nut. That nut will only do two turns on the shaft and then sticks. Turns out it has a fine thread pitch of 1.5 mm instead of the standard 2.5 mm for M20 bolts. So again, I email the manufacturer who say that they unfortunately do not have the correct type of nut in stock. But, they could send me a blank one, which I could then cut the correct thread into myself (free of charge!). Now all I need is someone with an M20 thread cutter who can make this blank into a useful part.
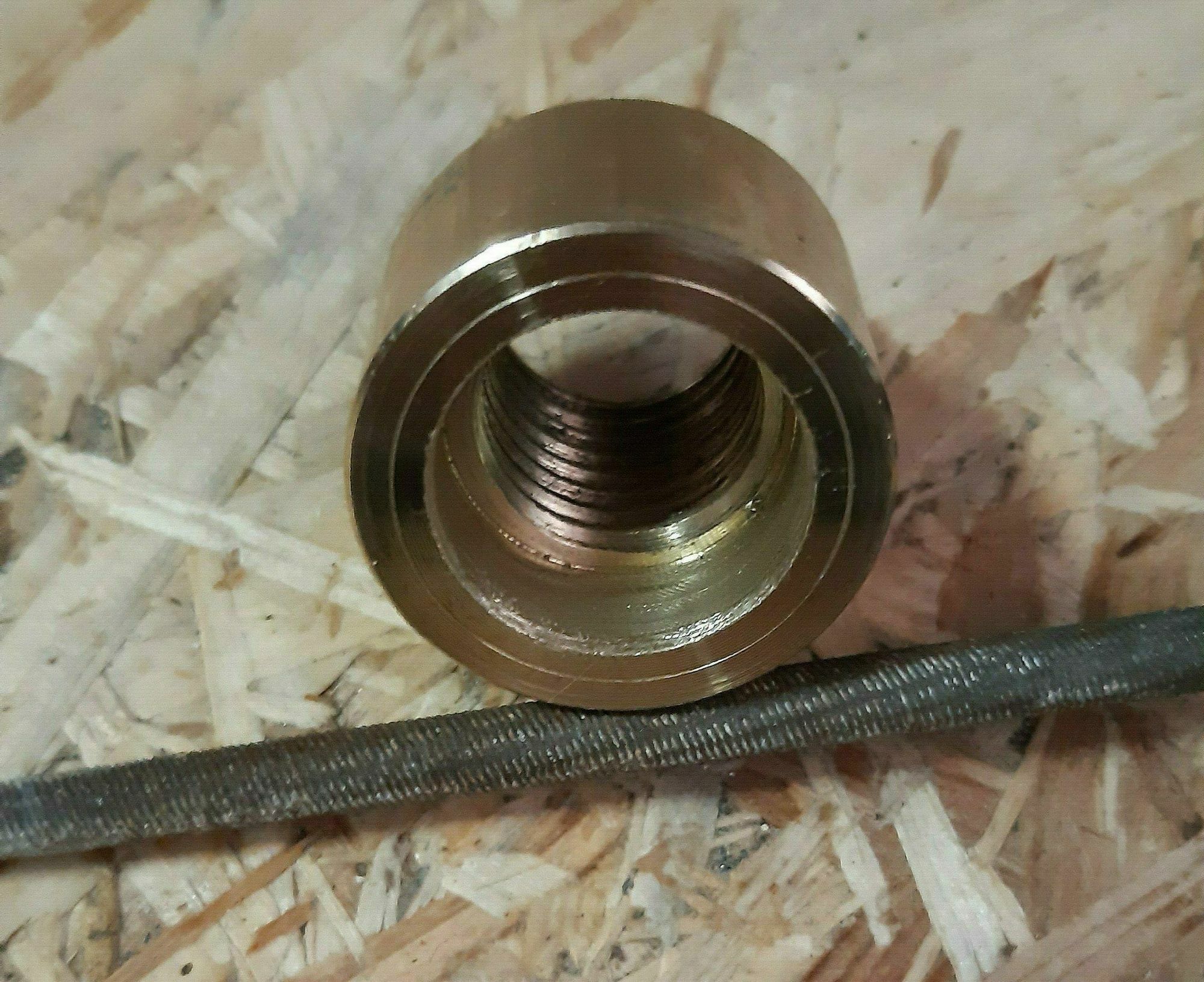
Enter Gerrit Trüschel from Trüschel Metalbau, who kindly helped us out and cut a thread fitting our shaft by hand. Feeling confident I take nut straight away to test out on the boat, but alas; the thread on the shaft is not long enough.
Back to Gerrit, who has to cut away 9 mm of his hard work to make everything fit together. After a little bit more filing in the boat shed, the hub finally is on its proper position on the shaft, but of course the key way sizing doesn't match. The propeller has a 8 mm key way and the shaft 10 mm, a small but significant difference.
Once again, guess who come to he rescue with a CNC mill?
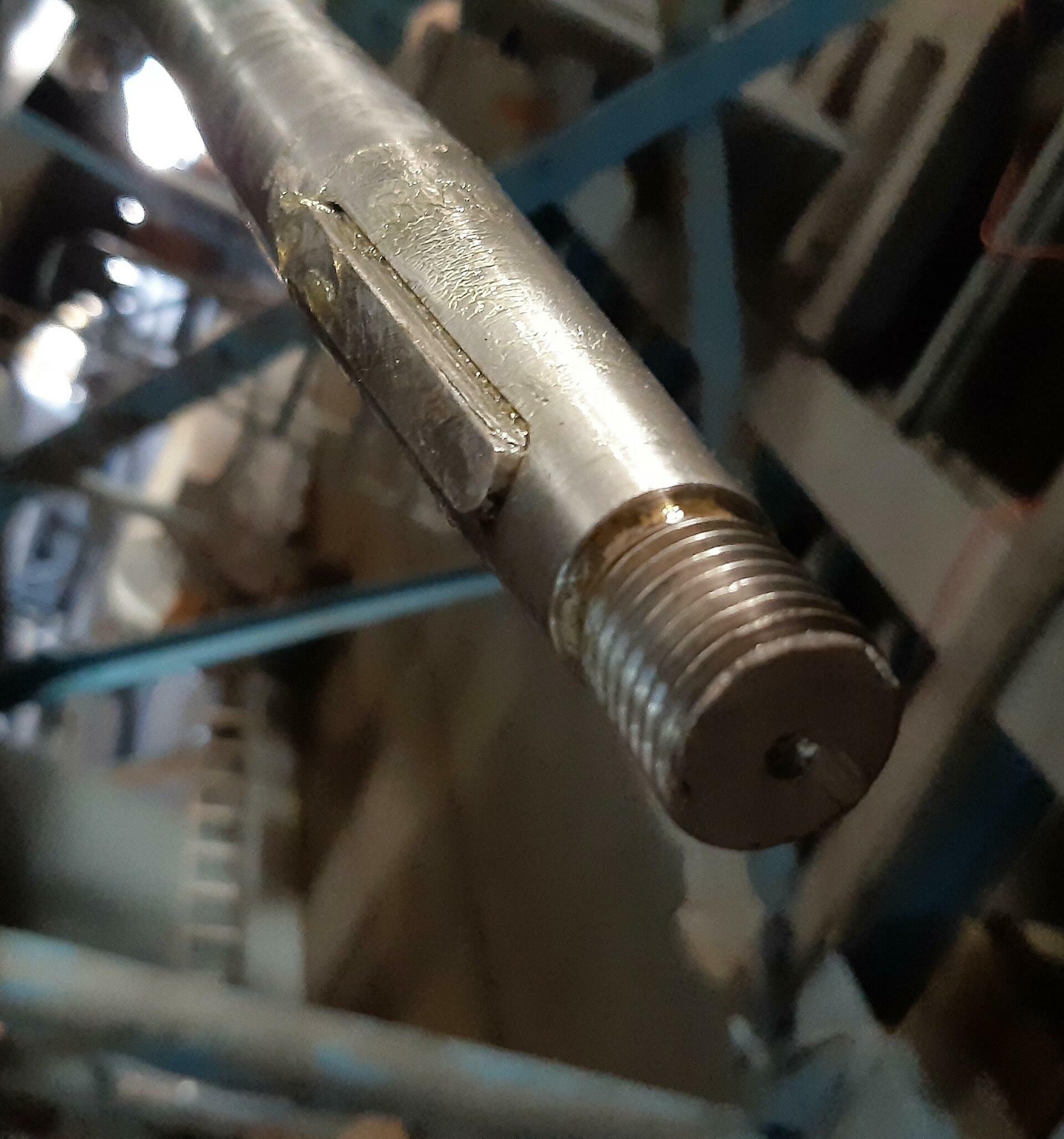
Just 1 by 3 mm off of each side and we have a special adaptor key to fit this new propeller on to our old shaft.
Finally I had to remove the last 9 mm of the shaft to make room for the folding mechanism's gears.
This propeller will push us forward when it turns clockwise and pull us backwards turning anti-clockwise; exactly opposite to the old one. In order to make the gear lever point in the correct direction we need to reverse its action, which can be done by flipping the gear actuator of the morse lever.
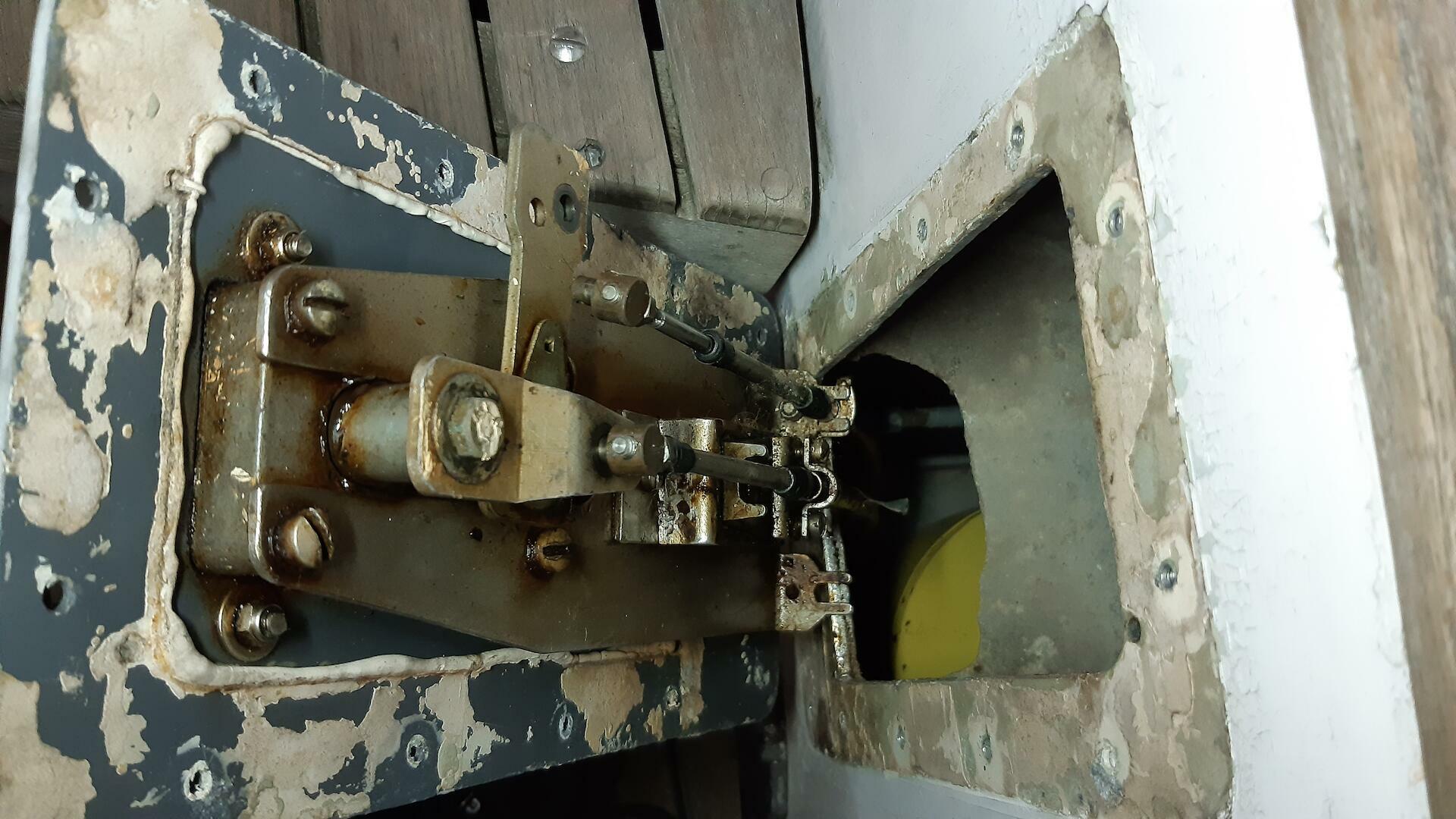
Finally the propeller is in its proper place, but this experience goes to show that it is not always easy to fit new parts to old boats!